Kia Optima: Front View Camera System / Front View Camera Unit
Schematic diagrams
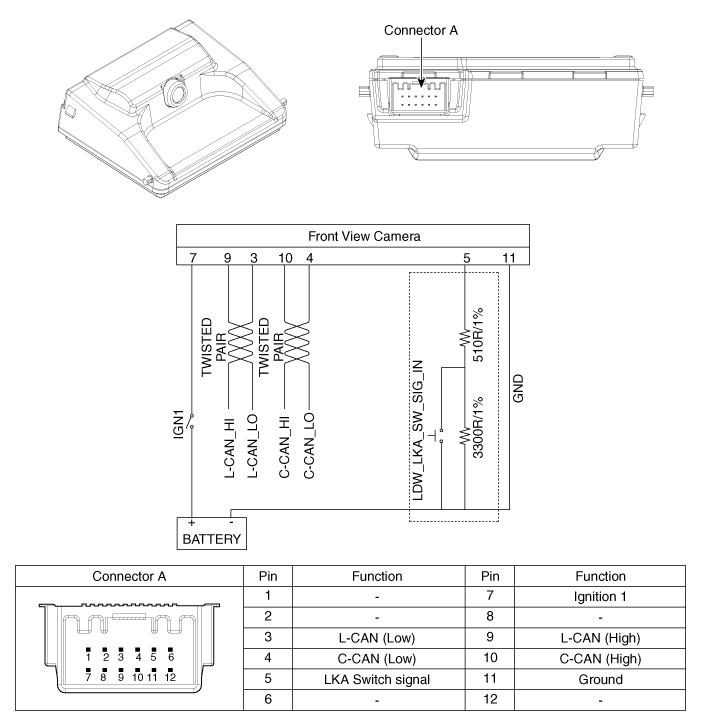
Repair procedures
1. |
In the body electrical system, failure can be quickly diagnosed by using
Kia Diagnostic System (KDS).
The diagnostic system (KDS) provides the following information.
(1) |
Self diagnosis : Checking failure and code number (DTC).
|
(2) |
Current data : Checking the system input/output data state.
|
(3) |
Actuation test : Checking the system operation condition.
|
(4) |
Additional function : Controlling other features including system
option setting and zero point adjustment.
|
|
1. |
You should read the specification information for the front view camera
that is installed in the vehicle before replacing it with a new front view
camera.
(1) |
Connect the VCI-II wireless adapter to the Data Link Connector
(DLC) in driver side crash pad lower panel, and turn on KDS.
|
(2) |
Select the 'S/W Management' and 'Car model'.
|
(3) |
Select "Front View Camera" and "System Identification".
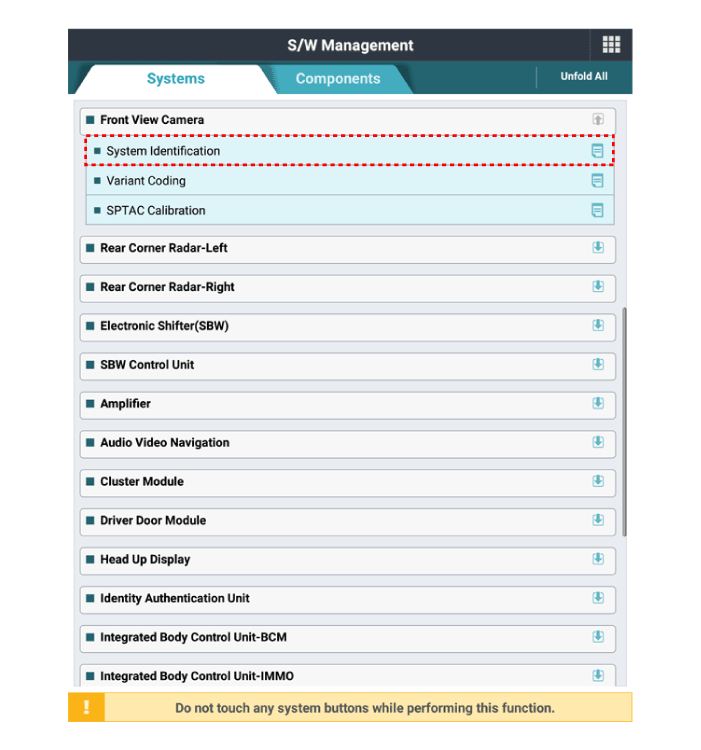
|
|
2. |
Disconnect the negative (-) battery terminal.
|
3. |
Remove the inside rear view mirror cover (A) and unit cover (B).
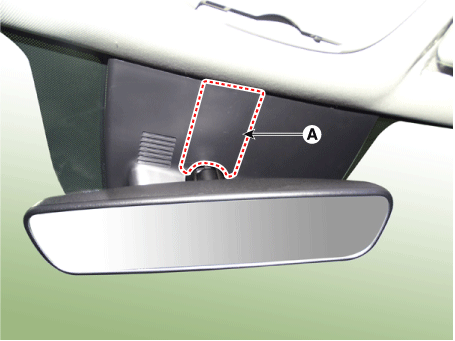
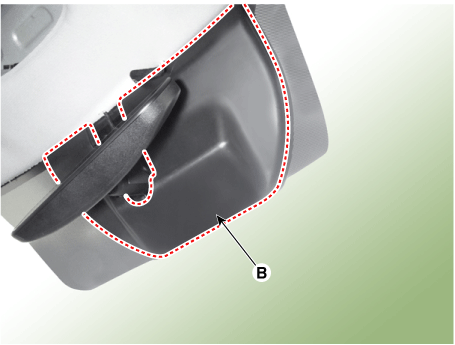
|
4. |
Disconnect the front view camera connector (A).
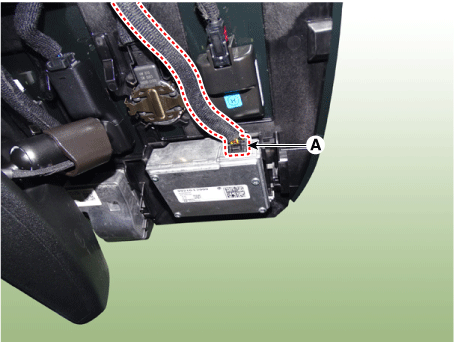
|
5. |
Separate the fixed points (A) of coupler, remove the front view camera
(B).
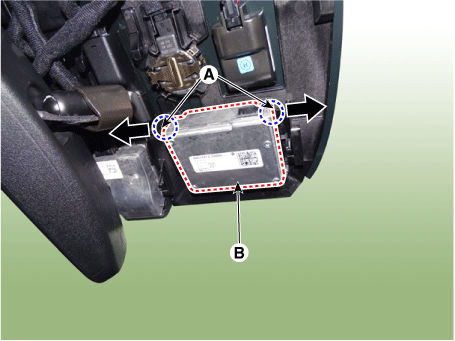
When separate the fixed points (A), be careful not to damage
it.
|
|
1. |
Install in the reverse order of removal.
•
|
Align the reference point at alignment point (A) and
align front view camera.
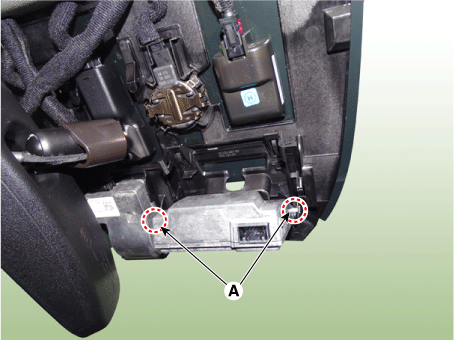
|
•
|
Fully assembly so that you can hear a "clicking" sound
when assembling.
|
|
|
2. |
When replacing the front view camera with a new one, perform the "Variant
Coding" procedure using KDS.
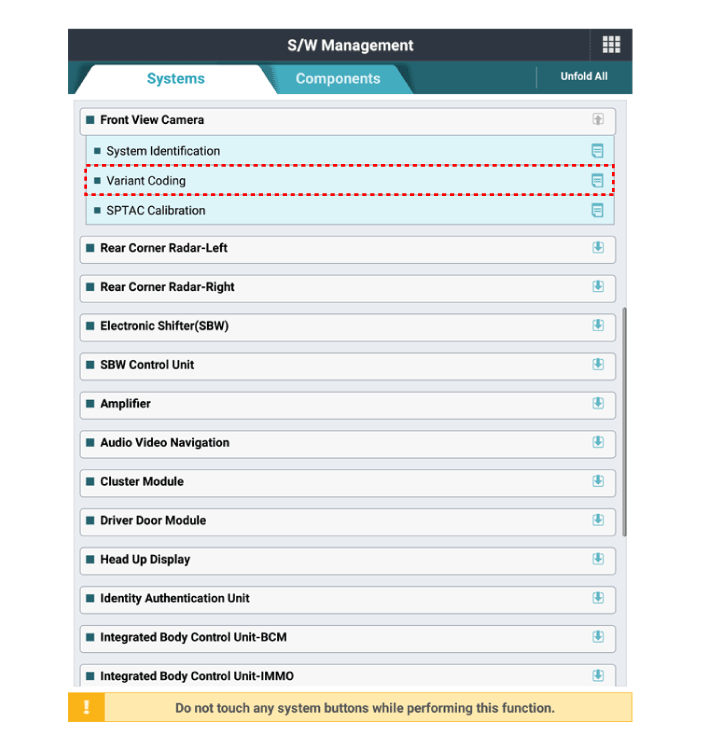
|
3. |
Perform the front view camera unit calibration.
(Refer to Front View Camera Unit - "Adjustment")
|
Perform the camera calibration in the following case.
• |
If the front view camera is replaced with a new one.
|
• |
If the front view camera is removed and mounted.
|
• |
If the front view camera coupler of the windshield glass is deformed.
|
• |
If the windshield glass is changed.
|
• |
When a failure code (System Out of Calibration) occur.
|
Check the procedure below before performing the camera calibration.
• |
Check for vehicle alignment and tire pressure for accurate camera
calibration.
|
• |
Windshield must be clean and free of any dirt or object.
|
|
Service Point Target
Auto Calibration (SPTAC) Procedure
1. |
Install the SST (09964-C1200) on the roof center above the vehicle's
front windshield.
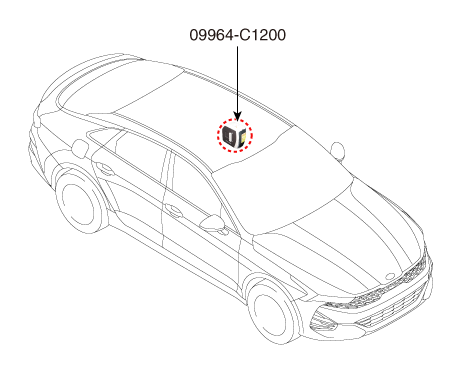
|
2. |
Have the laser illuminate starting from the roof center and to passing
through the center of the emblem.
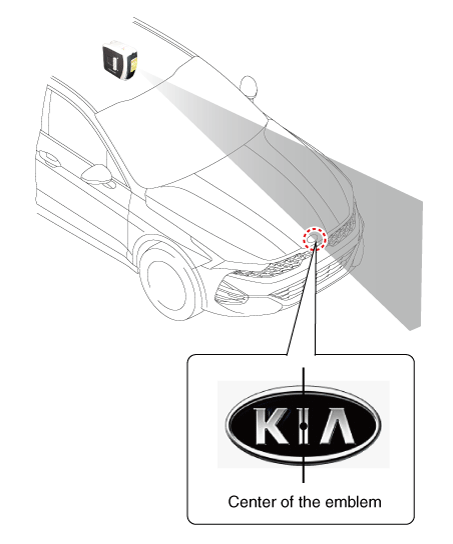
The level laser must be set to 'ON' and the holding (locking)
function is not used.
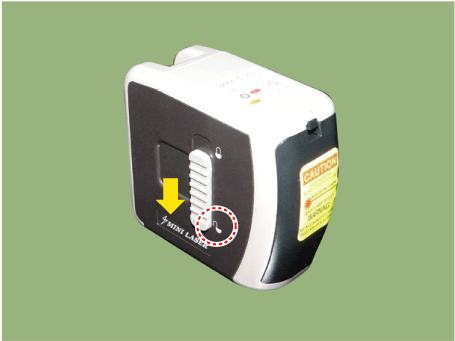
|
|
3. |
Place the calibration target (09890-3V100) so that it adheres by 0 cm
to the bumper front. [max. tolerance: 5 cm (1.97 in.)]
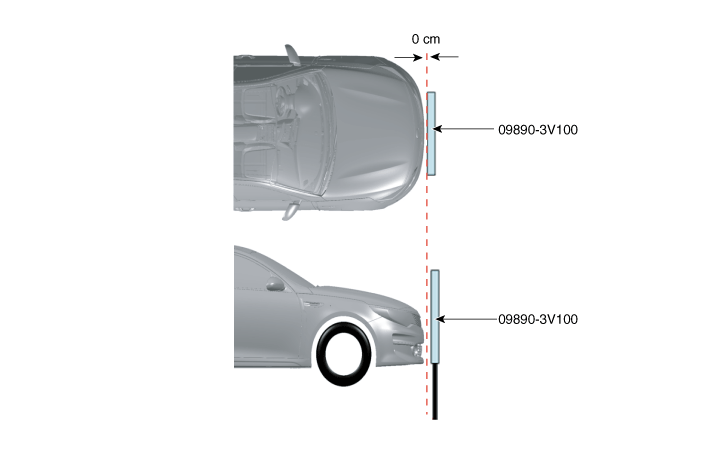
|
4. |
Set the calibration target height to 90 ± 1 cm (35.43 ± 0.39 in.) from
the ground and align the center of calibration target with center line (A)
of laser beam.
The target is placed along the vehicle’s longitudinal axis (centerline)
within ± 3cm (± 1.18 inch) of target center.
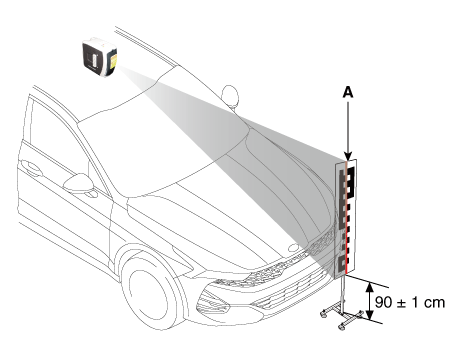
•
|
The vehicle horizontal plane shall be completely parallel
to the target horizontal plane (± 1degree).
|
•
|
Align the calibration target (09890-3V100) referring
to the tolerance angle below.
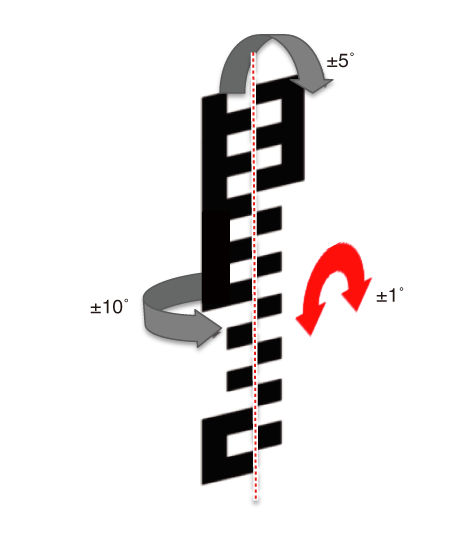
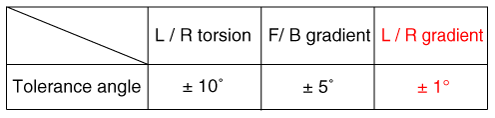
|
•
|
Mounting area must not have cross hatch patterns or textual
markings near the target.
|
•
|
Target should be well lit for optimal performance using
non-fluctuating illumination. There shall be no continuous
shadows cast on the target.
|
•
|
The light should be directed toward the target front
and the target front should be brighter than the target
rear and target.
|
|
|
5. |
Perform the "SPTAC Calibration" using the KDS.
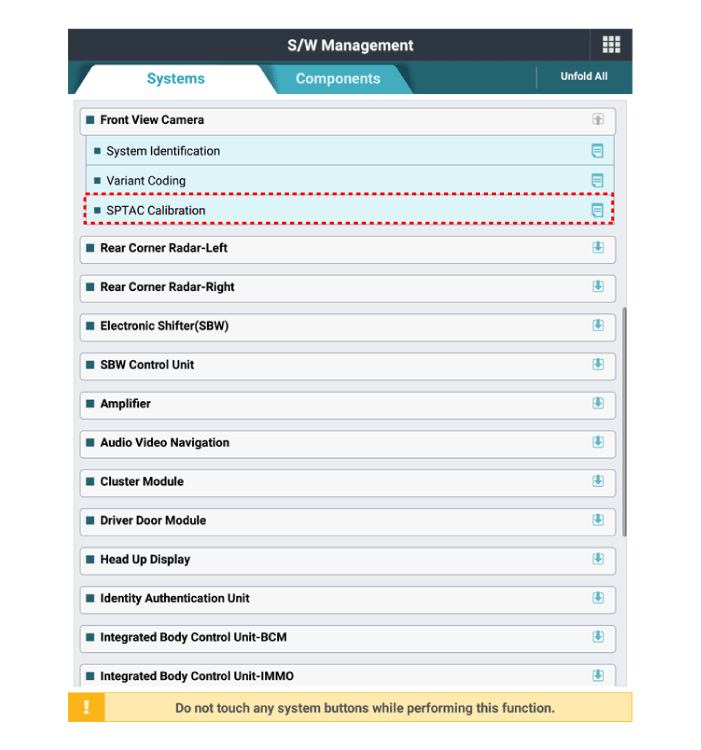
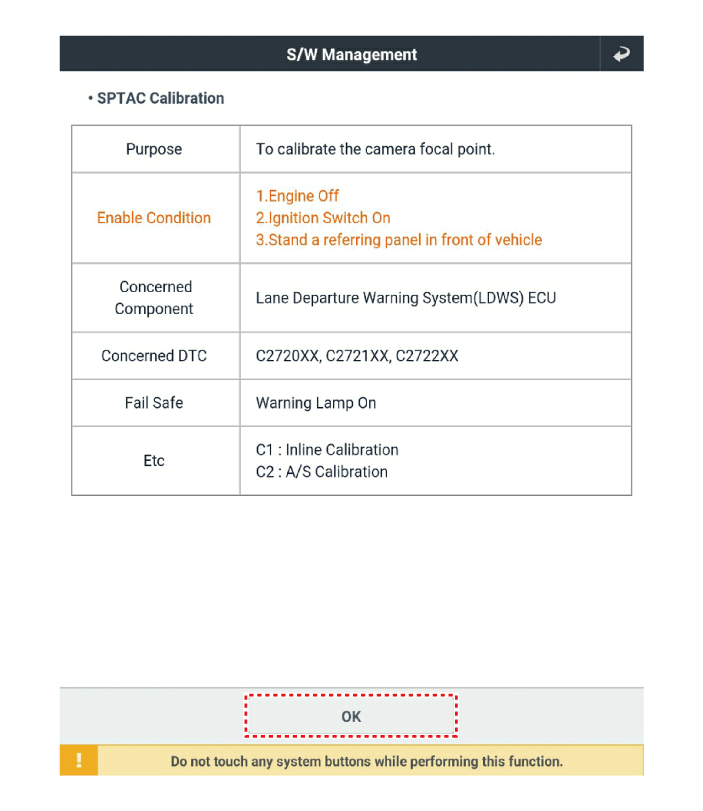
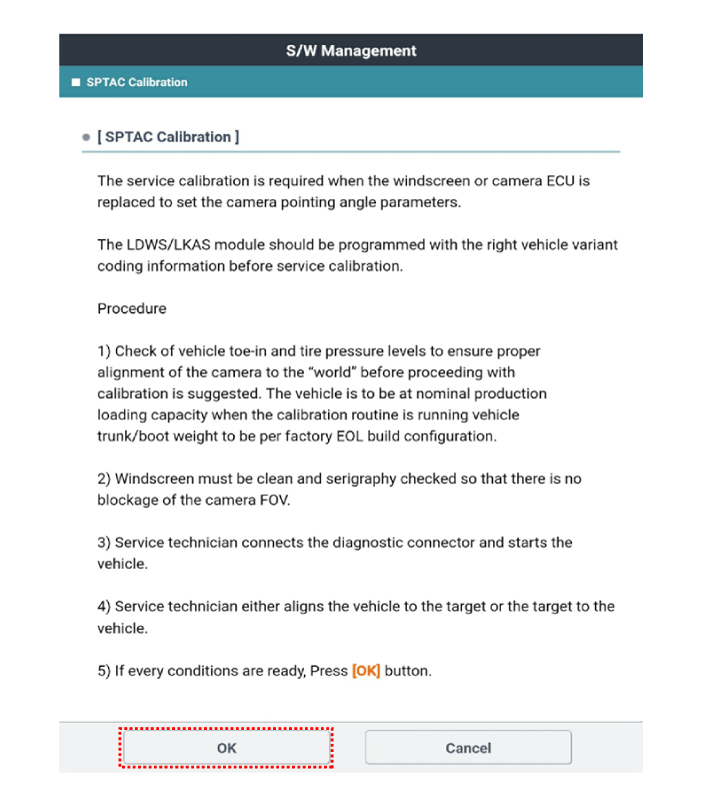
|
6. |
Perform the short-distance calibration by selecting the "OK" message
on the KDS after checking the calibration target location.
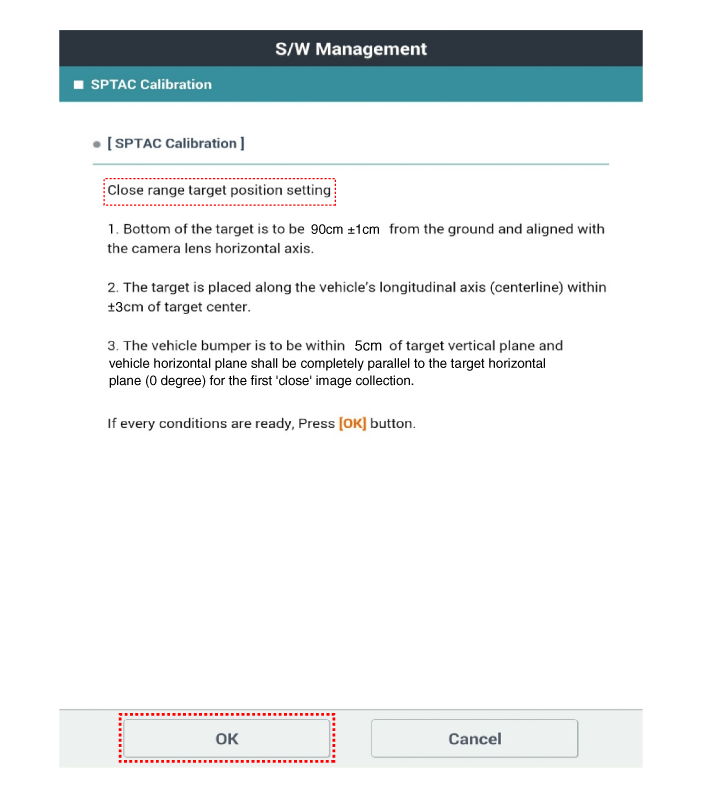
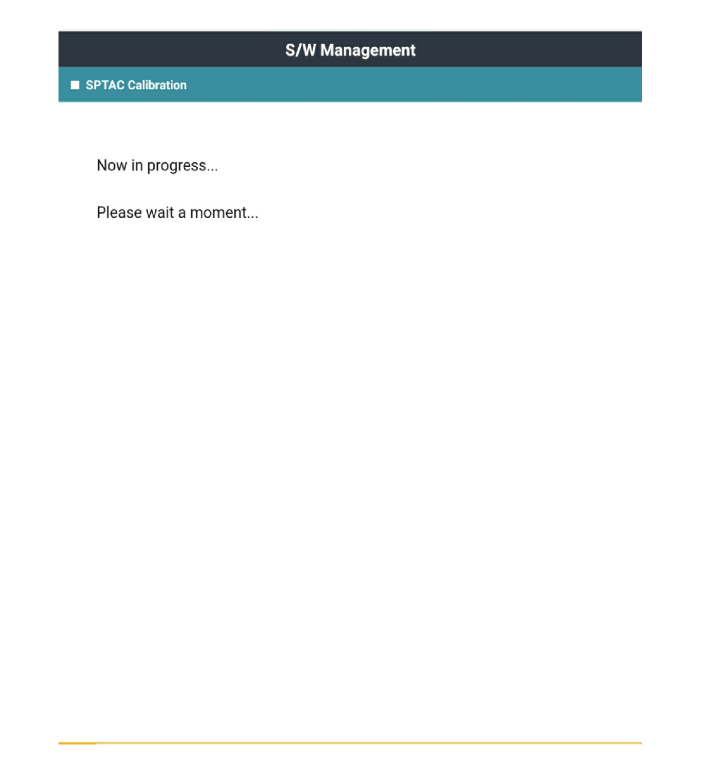
|
7. |
Move the calibration target (09890-3V100) at 100 cm (39.37 in.) from
the bumper. [max. tolerance : ± 5 cm (± 1.97 in.)]
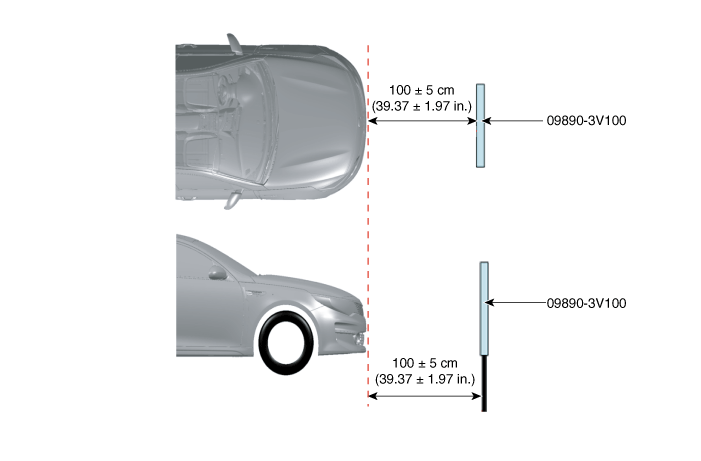
|
8. |
Set the calibration target height to 90 ± 1 cm (35.43 ± 0.39 in.) from
the ground and align the center of calibration target with center line (A)
of laser beam.
The target is placed along the vehicle’s longitudinal axis (centerline)
within ± 3cm (± 1.18 inch) of target center.
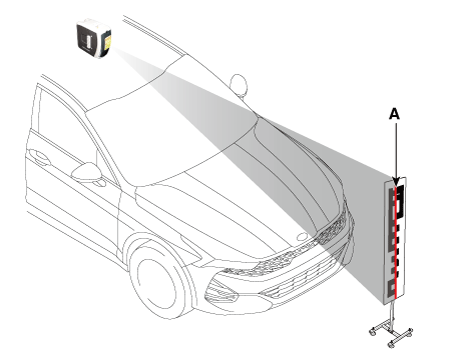
•
|
The vehicle horizontal plane shall be completely parallel
to the target horizontal plane (± 1degree).
|
•
|
Align the calibration target (09890-3V100) referring
to the below tolerance angle.
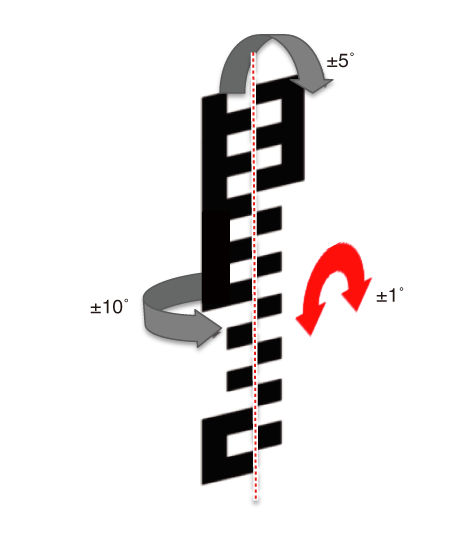
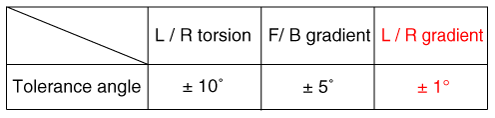
|
•
|
Mounting area must not have cross hatch patterns or textual
markings near the target.
|
•
|
Target should be well lit for optimal performance using
non-fluctuating illumination. There shall be no continuous
shadows cast on the target.
|
•
|
The light should be directed toward the target front
and the target front should be brighter than the target
rear and target.
|
|
|
9. |
Perform the long-distance calibration by selecting the "OK" message on
the KDS after checking the calibration target location.

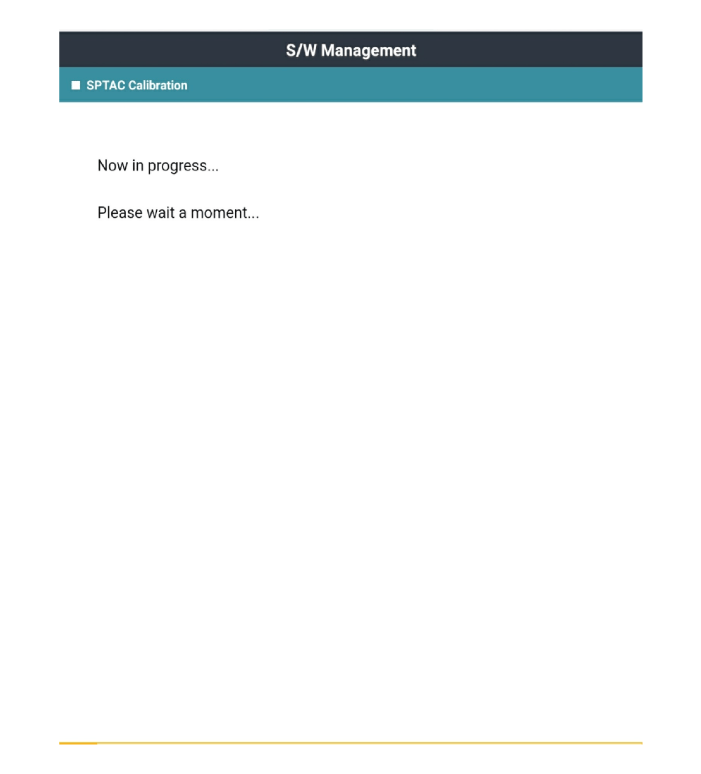
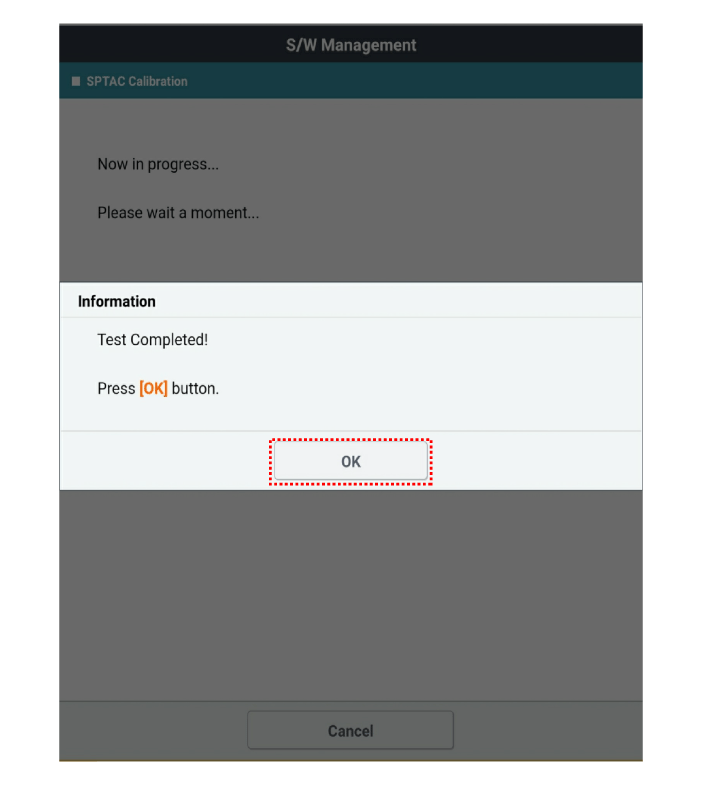
|
10. |
Clear the diagnostic trouble codes (DTC) using the KDS.
|
11. |
Check the DTC and warning lamp.
|
Components and components location
Components Location
1. Front view camera
2. AVN Head unit
3. Cluster
4. LFA,SCC ON/OFF switch (Remote
control switch) ...
Schematic diagrams
Connector and Terminal Function
Repair procedures
Inspection
1.
Disconnect the negative (-) battery terminal.
2.
...
Other information:
Operating condition
This system will activate when the indicator on the parking distance warning-reverse
OFF button is not illuminated. If you desire to deactivate the parking distance
warningreverse, press the parking distance warning-reverse OFF button again.
(The indicator on the but ...
Components and components location
Components
1. Crankshaft upper bearing
2. Crankshaft thrust bearing
3. Crankshaft
4. Crankshaft lower bearing
5. Crankshaft position sensor
(CKPS) wheel
6. Lower crankcase
7. Gasket
Repair p ...